Stop work orders, don’t wait. They hit hard—freeze your site, halt your schedule, and light a match under your budget. And they don’t come with a pause button. You’ve got inspectors, deadlines, fines, and a paper trail that can spiral out of control if you let it. And let’s be real, most people aren’t ready for it when it happens.
Some scramble. Others guess. The smart ones follow a proven playbook. This guide is that playbook. We’re not here to tell you what a stop work order is. If it’s landed on your project, you already know. What matters is clearing it fast—and doing it right, without creating more problems than you solve.
You’ll learn:
- Why do work orders get issued in the first place—and how to spot one before it hits.
- The exact steps to lift a stop work order fast, without costly delays.
- How to gather and file the right documents (and who needs to see them).
- The role of violation resolution tools like ViolationWatch in cutting your response time.
This is the straight-line fix to a problem that costs time, money, and credibility. Let’s walk through it.
What Triggers a Stop Work Order—and How to See It Coming
A stop work order never shows up at random. It’s triggered by something—something specific, traceable, and preventable. And if you’re paying attention, the warning signs always show up before the paperwork does.
Let’s break this down clearly.
The Most Common Triggers
Here’s what actually causes a stop work order to get issued:
- Unpermitted work: Work begins before the necessary permits are issued or posted. That includes structural, mechanical, plumbing, and even minor alterations. This often happens when the appropriate technician or contractor is left out of the approval loop.
- Permit violations: You have a permit, but you’ve strayed from the approved plans, missed permit conditions, or failed inspections tied to the job. These missteps stall task completion and invite formal enforcement.
- Unsafe site conditions: Exposed wiring. Open shafts. Incomplete scaffolding. Missing guardrails. Inspectors don’t ignore life safety issues. If it’s hazardous, work stops. These risks often trace back to skipped checks or neglected proactive maintenance protocols.
- Improper contractor licensing: Work gets flagged when unlicensed or improperly classified contractors are performing tasks that require specific credentials. Always verify that the qualified technician assigned is properly registered with the city.
- Noise or community complaints: Working outside permitted hours or triggering community complaints can lead to surprise inspections and fast enforcement. A streamlined task management system helps prevent repeated complaints that compound into full stops.
- Failure to comply with prior violations: If there’s already an open violation that’s been ignored or partially addressed, enforcement agencies may escalate to a stop-work order. This is especially true in cases of illegal construction where prior correction orders were never fully closed.
Each of these is a compliance breakdown. Not all are intentional, but they all carry weight.
Early Warning Signs
The good news? You can spot most of this before the order hits your site. Here’s how:
- Frequent site inspections or re-inspections: If inspectors keep showing up without a clear reason, there’s usually a red flag in your file or a complaint on record. Smart teams use performance tracking to spot trends before they become formal violations.
- Open violations that haven’t been cleared: One unresolved violation can tip off enforcement teams that compliance isn’t a priority. That’s when escalation begins—and where further penalties begin to stack.
- Permit or license expiration approaching: It’s easy to lose track of expiration dates. But once they lapse, your work becomes unauthorized, whether it’s been safe or not. Set automated reminders or leverage tools that support automated work order creation to avoid these lapses.
- Community boards or neighbors raising issues: When complaints surface, enforcement gets triggered faster than most project managers expect. Noise. Dust. Trash. Even delivery timing. A responsive maintenance team trained in troubleshooting techniques can minimize these incidents before they spiral.
- Requests for additional documents or plan revisions: That’s a quiet sign that your original paperwork is under scrutiny, and your next misstep might halt everything. Use that window to track progress, close gaps, and push for continuous improvement in your filing workflow.
To stay ahead, smart operators schedule routine inspections internally, not just because they’re required, but because they reduce enforcement risks, support business processes, and contribute to customer satisfaction by keeping stakeholders informed. Mobile access makes it easier. Empower your field crews with mobile devices that let them update status, handle service requests, and document progress on the spot.
Catch these signals early, and you’re ahead of the problem. Miss them—and the next knock at your site might be enforcement. When you know what to watch, you don’t just stay compliant—you gain leverage.
How to Clear a Stop Work Order Fast Without Adding Delays
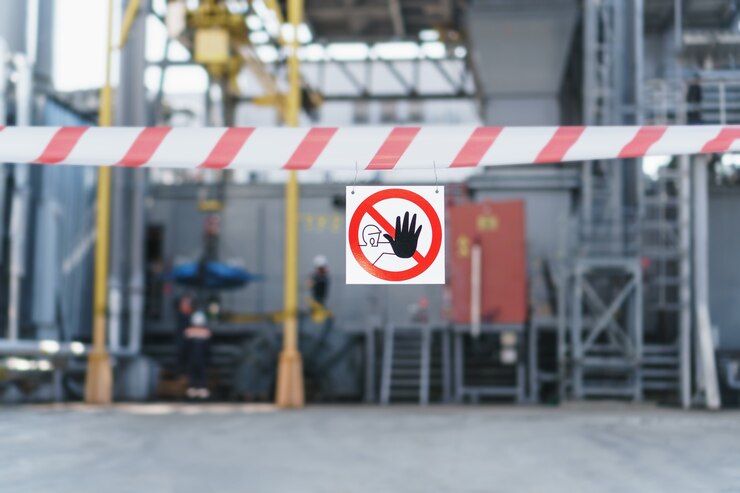
Getting hit with a stop-work order is stressful. But clearing it doesn’t have to be chaos. The process is structured—if you know what to do and who to deal with. Every hour counts. Each missed form, skipped inspection, or wrong contact sets you back. The faster you work through these steps, the sooner your job site gets moving again.
Step 1 — Identify the Root Violation
Start by pulling the stop work order from the issuing agency’s portal—typically DOB NOW or BIS for DOB-issued orders. Match the order number with the full violation record. Look for the infraction code, description, inspection details, and issuing officer’s notes.
You’re not just looking for what triggered the stop—you’re building a violation map. This includes:
- Permit status review: Was work performed without an approved PW1? Were TR1/TR8 forms filed correctly?
- Work scope mismatch: Does the stop work reference tasks not covered by the approved Schedule A or Schedule B?
- Previous open violations: An open ECB or HPD violation tied to the BIN can escalate into a stop work if ignored for too long.
If the root cause is unclear or the violation appears misclassified, request a copy of the inspector’s field report. You can also contact the borough enforcement office for clarification, which may reveal additional compliance obligations (e.g., FDNY permits, DOT approvals, etc.).
Step 2 — Notify All Relevant Parties
This isn’t a formality. It’s a tactical move to align every contributor involved with site compliance. You must notify:
- General contractor (GC)
- Registered design professional (RDP) — either the architect or engineer of record
- Owner of record or property manager
- Expeditor or filing rep
- Site safety coordinator (if required under BC Chapter 33)
- Third-party special inspectors (e.g., for concrete, plumbing, energy code compliance)
Share the full stop work order, associated violations, and deadlines. Request written confirmation from each party on the following:
- Which compliance items are they responsible for
- When and how they’ll address their portion
- What documents or corrections do they need to provide
Delays often stem from one party being unaware they’re on the hook for a filing or field correction.
Step 3 — Correct the Cited Issue
Now the real work begins. Correcting the issue means fully resolving the condition that triggered the order, not applying a cosmetic fix. Depending on the violation, this could involve:
- Structural work: If unauthorized framing or support changes were made, updated plans stamped by a PE must be filed with the DOB, along with a structural stability letter.
- Permit correction: Submit a post-approval amendment (PAA) if the work deviated from the original filing. This might include revised Schedule B, energy analysis, or new TR1 inspections.
- Life safety remediation: Issues like unsecured scaffolds, missing guardrails, or improper egress routes must comply with BC 3303 and be corrected per OSHA standards.
- Unlicensed work: If plumbing or electrical work was performed without a licensed subcontractor, remove the work, hire a licensed professional, and re-do under their permit.
All corrections must be documented with:
- Dated, geo-tagged photos
- Contractor sign-offs
- Material receipts or invoices
- Updated plan sheets if required
Treat this like an audit file—any missing element could delay your re-inspection approval.
Step 4 — Schedule a Re-Inspection
Before you request a re-inspection, confirm eligibility through the issuing agency’s portal. Some violations require you to submit a Certificate of Correction (AEU2 form) before the inspector will return.
Here’s what to do:
- Log the correction online through DOB NOW: Safety or BIS, depending on the issuing unit (Construction Safety Enforcement, Plumbing Enforcement, etc.).
- Upload documentation: Include photo proof, signed affidavits, and any professional letters of correction.
- Request the re-inspection through the agency’s dedicated request form or portal. Make sure to reference the original violation number and complaint ID.
For HPD or FDNY-related orders, additional fire-safety signoffs or inspections may be required. If the violation affects multiple floors or systems (e.g., HVAC), expect a multi-phase inspection process.
Tip: Have your GC or safety coordinator walk the inspector through the site, highlighting corrected conditions and supporting documents in person.
Step 5 — Submit the Required Paperwork
This is where even seasoned professionals get tripped up. Each agency has its own paperwork requirements tied to lifting a stop-work order. Here’s what you may need to file, depending on the issuing department:
- Certificate of Correction (AEU2) — for DOB violations, must be notarized
- TR1/TR8 inspection reports — to confirm completed inspections (concrete, plumbing, energy code, etc.)
- Updated Schedule A or B (PAA filing) — if the job scope changed
- Site Safety Plan sign-off — if applicable under the DOB’s Site Safety Unit
- Special inspection letters — for structural, waterproofing, underpinning, or fire suppression systems
- Notarized contractor and owner affidavits — affirming completion of corrective work
- Permit reinstatement requests — if any permits were revoked or expired during the SWO period
Use the DOB NOW portal or the HPD Online Services portal to submit these documents. Always save confirmation receipts and submit follow-ups if no update occurs within the agency’s stated timeline (typically 5–10 business days).
Step 6 — Pay Any Required Fees
Lifting a stop work order isn’t free. Common fees include:
- DOB civil penalties for work without a permit (up to $6,000 for initial violation + $1,000 monthly continuing penalty)
- Inspection fees for after-hours or re-inspections
- HPD or FDNY processing fees, depending on violation class
- Permit reactivation fees, if the job was dormant or revoked
Use DOB NOW: Pay Now, eFiling, or direct payments at the borough office. Never assume your fee is processed until it’s posted to the violation record.
If you’re working with a bonded violation, check whether a surety bond payout has already been applied, which may offset some fees but create separate obligations.
Step 7 — Confirm the Stop Work Order Is Lifted
You’re not done until the order status changes in writing.
- Log in to DOB NOW or BIS and confirm that the status of the stop work order is marked “RESCINDED” or “LIFTED.”
- Cross-reference the specific BIN and violation number—multiple violations on a single property can cause confusion.
- Download the updated record for your compliance file.
- Notify all project stakeholders, including contractors and consultants, that work can resume.
Don’t assume verbal confirmations are enough. Field inspectors might tell you it’s lifted, but unless the system reflects that change, enforcement can still act.
Get Your Paperwork in Order Before the Clock Works Against You
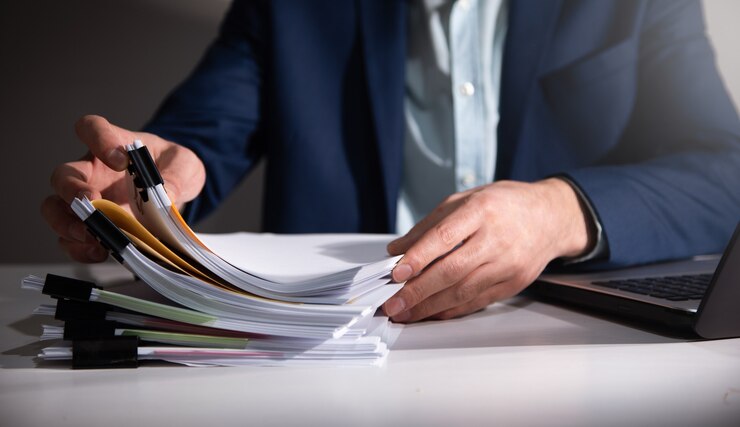
Filing the wrong document—or sending the right one to the wrong place—won’t just slow things down. It can lock your site in limbo for weeks. The agencies involved in stop work orders want precision. Each one requires specific documents, filed in a specific way, often by a specific party. Get it right, and the order moves. Get it wrong, and you stall.
Here’s how to handle documentation the right way.
Start With the Violation Source
Every agency has its own filing protocol. That means you’ll need to first identify who issued the stop work order and which department is enforcing it.
- DOB violations require coordination through DOB NOW and BIS
- HPD violations use their online compliance portal and may require paper submission
- FDNY violations may trigger mandatory inspection reports and affidavits
- ECB-related violations need a compliance filing with OATH and possibly civil penalty payment before resolution
Match the issuing agency with the documents they accept—and the format they want.
Build a Master List of Required Documents
At minimum, most stop work resolution files will include:
- Certificate of Correction (DOB/AECB): Often requires a notarized statement from the owner or contractor outlining the correction and evidence of the completed fix.
- Contractor Affidavit: Signed and notarized form confirming the work was corrected per code.
- Photographic Evidence: Clear, dated images showing before-and-after site conditions. These must be uploaded digitally and may also be required in hard copy.
- Inspection Sign-Off Reports: For anything that required reinspection—plumbing, structural, sprinkler, or energy code components.
- Updated Job Filings or Amendments (PAA): If work had to be refiled or modified, the updated Schedule A, B, and TR forms must be submitted before the violation clears.
- Letter from the Design Professional of Record: Especially for structural issues or changes involving code compliance, a PE or RA letter validating the fix is often mandatory.
- Permit Documents: Reissued permits or reinstated approvals must be filed with the resolution packet to demonstrate current compliance.
Each file should be indexed, timestamped, and backed up. Agencies do lose files, and delays happen when proof is missing.
Who Submits What?
Some forms are restricted. They must come directly from a licensed or authorized party. Here’s how responsibility breaks down:
Document Type | Submitted By |
Certificate of Correction | Owner or Owner Representative |
Contractor Affidavit | Licensed General Contractor or Sub |
TR1/TR8 Inspection Sign-Offs | Special Inspector or Filing Rep |
Professional Certification Letter | PE or RA (Design Professional of Record) |
Updated Plan Sheets or PW1 Amendments | Registered Filing Representative |
Fee Payments | Owner or Expediter |
Don’t let your team duplicate efforts or miss handoffs. Create a central point of contact to track all submitted documents and responses.
Where and How to File?
Each agency has a defined method of accepting documentation. The two most common platforms in NYC are:
- DOB NOW – Accepts Certificates of Correction, TR forms, PAAs, and supporting documents. Use the “Safety” or “Build” modules depending on the violation type.
- BIS (Building Information System) – Used for older filings or permits not yet transitioned to DOB NOW. Some documents require uploading via eFiling, then mailing originals.
- HPD Online Services – For housing-related violations, especially involving tenant complaints, maintenance failures, or lead/safety inspections.
- FDNY Business Portal – Required for permits, compliance letters, and scheduling follow-ups tied to life safety systems.
- DOT, DEP, DOH – Vary widely in submission style; always confirm with an agency rep whether documents must be emailed, uploaded, or mailed.
Always confirm delivery. Some systems auto-confirm. Others require manual follow-up. In either case, keep a hard copy and digital trail.
Filing is not a race. It’s a sequence. Submit too early—before fixing the core issue—and the entire correction can be rejected. Submit too late, and fees accumulate. The goal here is airtight documentation, submitted through the right channel, by the right person, with the right paper trail behind it. That’s what moves the order off your site.
How ViolationWatch Cuts Hours Off the Stop Work Clock
Time kills momentum. The longer a stop work order lingers, the more risk piles up—delays, penalties, unhappy owners, and blown budgets. ViolationWatch exists to cut that time down, step by step, hour by hour.
This isn’t a passive tracking tool. It’s a targeted resolution platform built for one thing: helping NYC property pros clear violations and move projects forward without guesswork. Here’s how it works when a stop work order lands on your site.
One Dashboard for Every Violation You’re Facing
Stop work orders rarely show up alone. They’re tied to violations from the DOB, HPD, ECB, FDNY, DEP, and other city agencies. ViolationWatch centralizes all those violations—building code violations, zoning violations, and fire safety violations—across multiple buildings into a single, live dashboard.
That means no flipping between BIS, DOB NOW, or HPD portals trying to piece together what went wrong and where it started. You can filter by building, agency, violation type, status, or urgency. What was fragmented becomes unified. That alone trims hours off your admin workload and improves operational efficiency.
Instant Alerts for New Violations, Hearings, and Status Updates
You don’t have to hunt for updates. ViolationWatch sends real-time alerts the moment a new violation is issued, a hearing is scheduled, or a compliance deadline hits. You’ll know when a Certificate of Correction is accepted—or rejected, when a follow-up inspection is scheduled. And when a civil penalty is about to be assessed.
That lets you move the right documents, coordinate with your team, and keep the job in motion before another stop work order stacks on top. This becomes especially useful for any assigned technician or maintenance department handling the site’s compliance response.
Automated Violation Tracking Means Fewer Errors
Manual tracking breeds mistakes. Deadlines get missed. Hearing dates slip through the cracks. ViolationWatch automates the entire tracking process. It monitors agency records, updates violation statuses, and flags next steps for each open item in your portfolio.
You can see what’s pending, what’s overdue, and what needs submission, without relying on email chains or old spreadsheets. That clarity helps teams stay focused, reduces unplanned maintenance, and supports accurate tracking of maintenance records.
Built-In Document Management Keeps Your Files Ready
Every stop-work resolution process depends on fast, complete documentation. ViolationWatch lets you store, tag, and organize all your documents—affidavits, correction forms, inspection reports, permits—inside the platform.
You can link files to specific properties, violations, or maintenance history records. That way, when an agency requests proof, it’s already there for future reference. No scrambling. No file hunting. No lost attachments. You also control who sees what—owners, contractors, attorneys, or filing reps—so you can delegate tasks without giving up oversight.
Compliance Experts on Standby When Things Get Messy
Some stop work orders spiral. Conflicting violations. Overlapping agencies. Stalled filings. ViolationWatch gives you access to real compliance professionals who understand the city’s systems inside and out.
Need help interpreting an inspector’s notes? Not sure which filing triggers a hearing extension? You can flag it—and get guided support from people who’ve done this across thousands of properties, including those dealing with code enforcement officers, safety protocols, or required corrective actions.
Portfolio Customization for Small and Large Operators Alike
Whether you’re managing one property or fifty, ViolationWatch scales with you. You can set up custom rules, alerts, and user access levels for each asset. That means whether you’re a solo manager or part of a city-wide team, the platform adapts to how you work.
You can also integrate it into broader maintenance operations, creating a more connected ecosystem between compliance and your maintenance software. For teams juggling routine inspections, work request logs, and reactive maintenance, that integration closes the loop.
Streamlined Workflows That Support Maintenance and Compliance
Because ViolationWatch integrates with your process, it helps tie preventive maintenance efforts directly to violation outcomes. Missed inspections become fewer. Paper trails get tighter. Deadlines are met, and workflows become repeatable.
For any team currently using spreadsheets or fragmented work order management software, that upgrade means smarter planning, faster execution, and better outcomes across compliance and facilities alike.
In short, ViolationWatch strips the friction out of the resolution process. No bottlenecks. No delays from scattered data. Everything’s tracked, filed, and flagged before the city comes knocking again. If your goal is resolving violations quickly while staying on top of every compliance and maintenance task, this is the system built to do it.
Resolve Stop Work Orders Faster With Less Guesswork
Lifting a stop work order isn’t just about following steps—it’s about minimizing fallout. Every delay adds friction. Every mistake costs money. But when you control the process, you control the outcome. You’ve now got a system that turns reaction into resolution. Not in theory—in practice.
What does that give you?
- Shorter downtimes — Crews get back to work sooner. Schedules recover faster.
- Fewer violations in the future — Because you’ve addressed the source, not just the symptom.
- Lower costs overall — Reduced penalties, cleaner filings, fewer failed inspections.
- Stronger working relationships — Contractors, architects, and stakeholders stop pointing fingers and start fixing problems.
- Proof you’re running a tight operation — Which matters when lenders, partners, or city inspectors come asking questions.
That’s the real outcome—operational control in a system that punishes disorganization. If you’re tired of jumping between portals, chasing paperwork, or missing updates that cost you days, ViolationWatch gives you the infrastructure to handle all of it in one place. With the right system behind you, stop work orders stop being setbacks—and start becoming solvable.